Metal to Plastic Conversions
NMC Dynaplas is a well-known for our reliable technical leadership in the conversion of functional /performance metal / aluminum / thermoset parts to recyclable thermoplastic.
Through close working relationships with performance polymer manufacturers, we are at advancing manufacturing with innovative tooling and processes. Resulting in us not just being on the edge of what is possible but creating it.
We work with our customers and the polymer resin manufacturers to find the right material for the application specifications, and we provide Design / Best Practices for Manufacturing expertise to make sure to confidently produce a high-quality, cost-effective part can be produced every time. Should component development and prototyping be the initial path forward, we are easily accessible and find creative solutions to support our clients goals every step of the way prior to serial production.
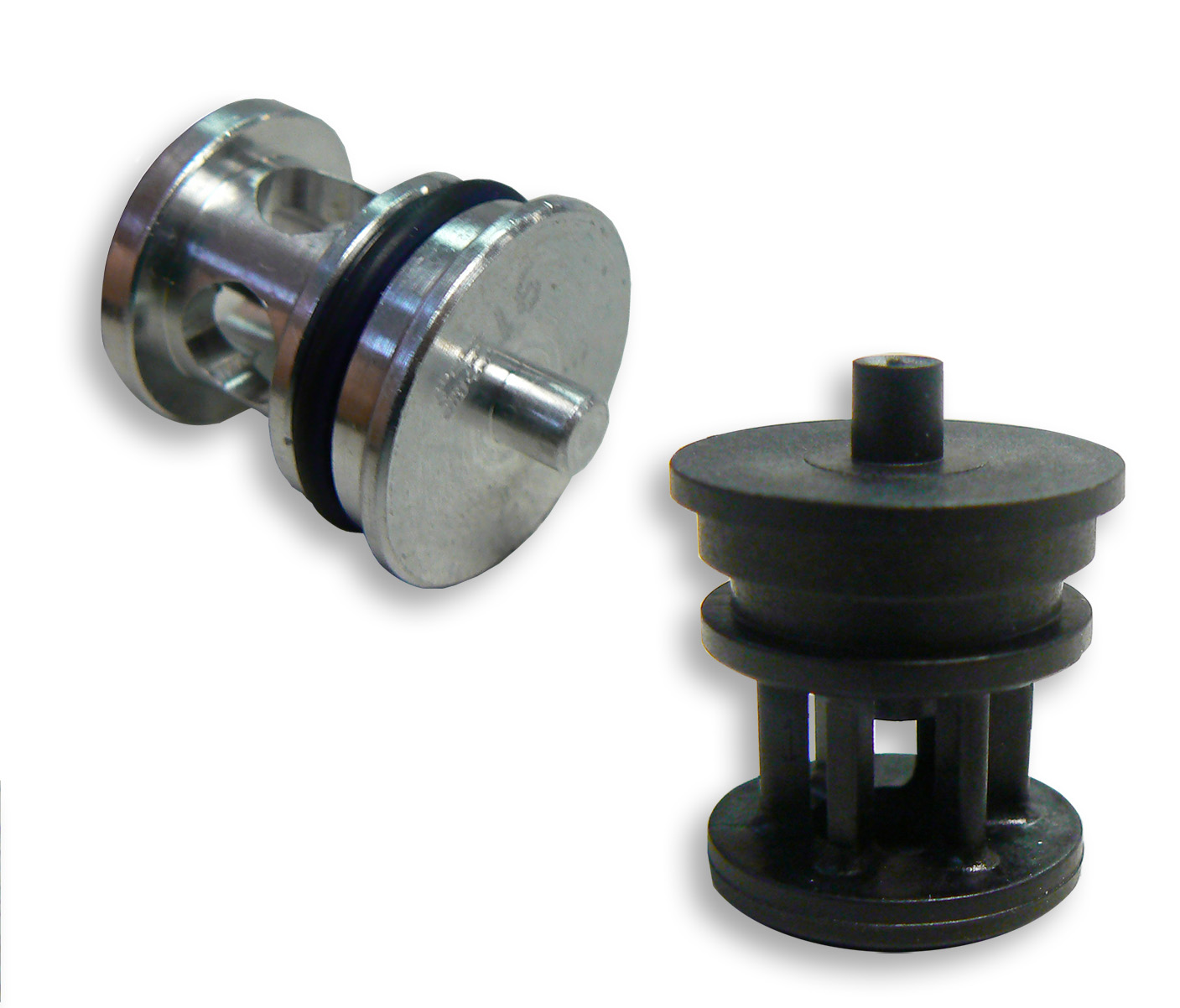
Improving Upon Metal
Our clients benefit from our conversion of critical parts from metal to thermoplastic, without sacrificing performance.
Some of the benefits of converting from metal to thermoplastic include:
- Reduced cost
- Part component (sku) consolidation
- Elimination of post machining operations/wasteful scrap
- Light weighting
- Increase recyclability
- Eliminate Corrosion resistance
- Reduced NVH in application
- Improve overall performance by incorporating design features not possible in casting, machining processes
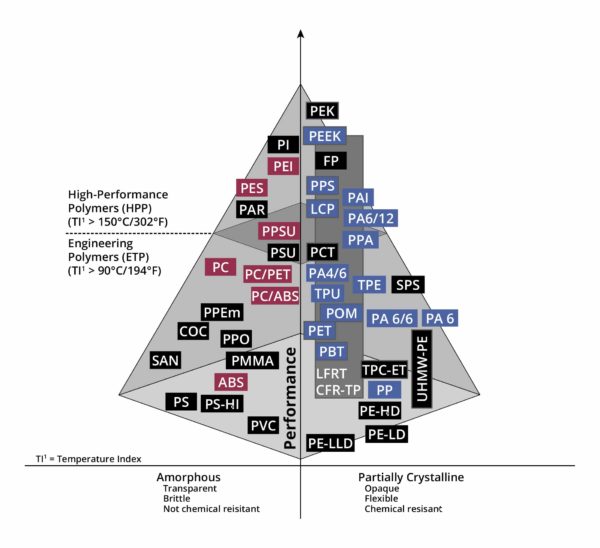
Optimizing Resin Performance
With a focus on performance resins, we optimize the injection molding process. Resins are compounded to include fillers or additives which alter properties and performance.
Characteristics include lubricity, stiffness, corrosion resistance, chemical inert, and electrostatic dissipation.
Resins We Use Include:
- PA (Polyamide-Nylon 6, 6/6, 4/6, 6/12)
- PBT (Polybutylene Terephthalate)
- PEEK (Polyether Ether Keytone)
- PEI (Polyetherimide)
- PES (Polyether Sulphone)
- POM (Acetal)
- PPA (Polyphthalamide)
- PPS (Polyphenylene Sulphide)
- PPSU (Polyphenylsulfone)
- PET (Polyethylene Terephthalate)
- TPE (Thermoplastic Elastomer)
- TPU (Thermoplastic Polyurethane)
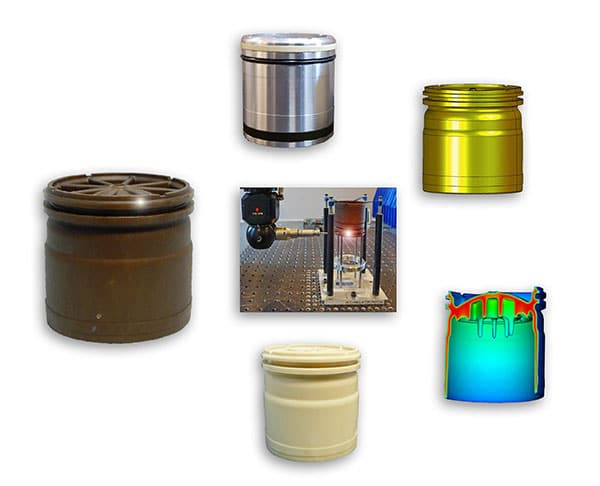
Case Study: Hydraulic Piston Material Conversion
Customer Challenge
- Maintain aggressive global pricing for energy saving systems
- Convert machined aluminum part with molded engineered thermoplastic
Technical Solution
- Consolidated three metal parts into one molded part
- One manufacturing process to produce final product
- Shorten manufacturing lead times and eliminate some assembly processes
Outcome
- Customer reduced inventory items (sku reduction)
- Significant cost savings of ~ 50% over three-piece version
- Eliminated labor intensive assembly process
- Performance enhancement – reduced energy (inertia required for system)
- Supporting customer global needs from North American and Asian manufacturing facilities